2019注册安全工程师《化工安全》第二章考点:重点监管的化工工艺及主要安全技术措施
时间:2021-12-24 14:03 来源:战考网
重点监管的化工工艺及主要安全技术措施(18类)
(一)光气及光气化工艺
1.反应类型:放热反应。
2.工艺危险特点:
(1)光气为剧毒气体,在储存、使用过程中发生泄露后,易造成大面积污染、中毒事故。
(2)反应介质具有燃爆危险性。
(3)副产物氯化氢具有腐蚀性,易造成设备和管线泄漏使人员发生中毒事故。
3.重点监控单元:光气化反应釜、光气储运单元。
4.宜采用的控制方式:
光气及光气化生产系统一旦出现异常现象或发生光气及其剧毒产品泄漏事故时,应通过自控联锁装
置启动紧急停车并自动切断所有进出生产装置的物料,将反应装置迅速冷却降温,同时将发生事故设备
内的剧毒物料导入事故槽内,开启氨水、稀碱液喷淋,启动通风排毒系统,将事故部位的有毒气体排至
处理系统。
(二)电解工艺(氯碱)
1.反应类型:吸热反应。
2.工艺危险特点:
(1)电解食盐水过程中产生的氢气是极易燃烧的气体,氯气是氧化性很强的剧毒气体,两种气体混合极易发生爆炸,当氯气中含氢量达到5%以上,则随时可能在光照或受热情况下发生爆炸。
(2)如果盐水中存在的铵盐超标,在适宜的条件(pH<4.5)下,铵盐和氯作用可生成氯化铵,浓氯化铵溶液与氯还可生成黄色油状的三氯化氮。三氯化氮是一种爆炸性物质,与许多有机物接触或加热至90℃以上以及被撞击、摩擦等,即发生剧烈的分解而爆炸。
(3)电解溶液腐蚀性强。
(4)液氯的生产、储存、包装、输送、运输可能发生液氯的泄漏。
3.重点监控单元:电解槽、氯气储运单元。
4.宜采用的控制方式:
(1)将电解槽内压力、槽电压等形成联锁关系,系统设立联锁停车系统。
(2)安全设施,包括安全阀、高压阀、紧急排放阀、液位计、单向阀及紧急切断装置等
(三)氯化工艺
1.反应类型:放热反应。
2.工艺危险特点:
(1)氯化反应是一个放热过程,尤其在较高温度下进行氯化,反应更为剧烈,速度快,放热量较
大。
(2)所用的原料大多具有燃爆危险性。
(3)常用的氯化剂氯气本身为剧毒化学品,氧化性强,储存压力较高,多数氯化工艺采用液氯生产是先汽化再氯化,一旦泄漏危险性较大。
(4)氯气中的杂质,如水、氢气、氧气、三氯化氮等,在使用中易发生危险,特别是三氯化氮积累后,容易引发爆炸危险。
(5)生成的氯化氢气体遇水后腐蚀性强。
(6)氯化反应尾气可能形成爆炸性混合物。
3.重点监控单元:氯化反应釜、氯气储运单元。
4.宜采用的控制方式:
(1)将氯化反应釜内温度、压力与釜内搅拌、氯化剂流量、氯化反应釜夹套冷却水进水阀形成联锁关系,设立紧急停车系统。
(2)安全设施,包括安全阀、高压阀、紧急放空阀、液位计、单向阀及紧急切断装置等。
(四)硝化工艺
1.反应类型:放热反应。
2.工艺危险特点:
(1)反应速度快,放热量大。
(2)反应物料具有燃爆危险性。
(3)硝化剂具有强腐蚀性、强氧化性,与油脂、有机化合物(尤其是不饱和有机化合物)接触能引起燃烧或爆炸。
(4)硝化产物、副产物具有爆炸危险性。
3.重点监控单元:硝化反应釜、分离单元。
4.宜采用的控制方式:
(1)将硝化反应釜内温度与釜内搅拌、硝化剂流量、硝化反应釜夹套冷却水进水阀形成联锁关系,在硝化反应釜处设立紧急停车系统,当硝化反应釜内温度超标或搅拌系统发生故障,能自动报警并自动停止加料。分离系统温度与加热、冷却形成联锁,温度超标时,能停止加热并紧急冷却。
(2)硝化反应系统应设有泄爆管和紧急排放系统。
(五)合成氨工艺
1.反应类型:吸热反应。
2.工艺危险特点:
(1)高温、高压使可燃气体爆炸极限扩宽,气体物料一旦过氧(亦称透氧),极易在设备和管道内发生爆炸。
(2)高温、高压气体物料从设备管线泄漏时会迅速膨胀与空气混合形成爆炸性混合物,遇到明火或因高流速物料与裂(喷)口处摩擦产生静电火花引起着火和空间爆炸。
(3)气体压缩机等转动设备在高温下运行会使润滑油挥发裂解,在附近管道内造成积炭,可导致积炭燃烧或爆炸。
(4)高温、高压可加速设备金属材料发生蠕变、改变金相组织,还会加剧氢气、氮气对钢材的氢蚀及渗氮,加剧设备的疲劳腐蚀,使其机械强度减弱,引发物理爆炸。
(5)液氨大规模事故性泄漏会形成低温云团引起大范围人群中毒,遇明火还会发生空间爆炸。
3.重点监控单元:合成塔、压缩机、氨储存系统。
4.宜采用的控制方式:
(1)将合成氨装置内温度、压力与物料流量、冷却系统形成联锁关系。
(2)将压缩机温度、压力、入口分离器液位与供电系统形成联锁关系。
(3)紧急停车系统。
(4)合成单元自动控制还需要设置以下几个控制回路:氨分、冷交液位;废锅液位;循环量控制;废锅蒸汽流量;废锅蒸汽压力。
(5)安全设施,包括安全阀、爆破片、紧急放空阀、液位计、单向阀及紧急切断装置等。
(六)裂解(裂化)工艺
1.反应类型:高温吸热反应。
2.工艺危险特点:
(1)在高温(高压)下进行反应,装置内的物料温度一般超过其自燃点,若漏出会立即引起火灾。
(2)炉管内壁结焦会使流体阻力增加,影响传热,当焦层达到一定厚度时,因炉管壁温度过高,而不能继续运行下去,必须进行清焦,否则会烧穿炉管,裂解气外泄,引起裂解炉爆炸。
(3)如果由于断电或引风机机械故障而使引风机突然停转,则炉膛内很快变成正压,会从窥视孔或烧嘴等处向外喷火,严重时会引起炉膛爆炸。
(4)如果燃料系统大幅度波动,燃料气压力过低,则可能造成裂解炉烧嘴回火,使烧嘴烧坏,甚至会引起爆炸。
(5)有些裂解工艺产生的单体会自聚或爆炸,需要向生产的单体中加阻聚剂或稀释剂等。
3.重点监控单元:裂解炉、制冷系统、压缩机、引风机、分离单元。
4.宜采用的控制方式:
(1)将引风机电流与裂解炉进料阀、燃料油进料阀、稀释蒸汽阀之间形成联锁关系,一旦引风机故障停车,则裂解炉自动停止进料并切断燃料供应,但应继续供应稀释蒸汽,以带走炉膛内的余热。
(2)将燃料油压力与燃料油进料阀、裂解炉进料阀之间形成联锁关系,燃料油压力降低,则切断燃料油进料阀,同时切断裂解炉进料阀。
(3)分离塔应安装安全阀和放空管,低压系统与高压系统之间应有逆止阀并配备固定的氮气装置、蒸汽灭火装置。
(4)将裂解炉电流与锅炉给水流量、稀释蒸汽流量之间形成联锁关系;一旦水、电、蒸汽等公用工程出现故障,裂解炉能自动紧急停车。
(5)反应压力正常情况下由压缩机转速控制,开工及非正常工况下由压缩机入口放火炬控制。
(6)再生压力由烟机入口蝶阀和旁路滑阀(或蝶阀)分程控制。
(7)再生、待生滑阀正常情况下分别由反应温度信号和反应器料位信号控制,一旦滑阀差压出现低限,则转由滑阀差压控制。
(8)再生温度由外取热器催化剂循环量或流化介质流量控制。
(9)外取热汽包和锅炉汽包液位采用液位、补水量和蒸发量三冲量控制。
(10)带明火的锅炉设置熄火保护控制。
(11)大型机组设置相关的轴温、轴震动、轴位移、油压、油温、防喘振等系统控制。
(12)在装置存在可燃气体、有毒气体泄漏的部位设置可燃气体报警仪和有毒气体报警仪。
(七)氟化工艺
1.反应类型:放热反应。
2.工艺危险特点:
(1)反应物料具有燃爆危险性。
(2)氟化反应为强放热反应,不及时排除反应热量,易导致超温超压,引发设备爆炸事故。
(3)多数氟化剂具有强腐蚀性、剧毒,在生产、贮存、运输、使用等过程中,容易因泄漏、操作不当、误接触以及其他意外而造成危险。
3.重点监控单元:氟化剂储运单元。
4.宜采用的控制方式:
(1)氟化反应操作中,要严格控制氟化物浓度、投料配比、进料速度和反应温度等。必要时应设置自动比例调节装置和自动联锁控制装置。
(2)将氟化反应釜内温度、压力与釜内搅拌、氟化物流量、氟化反应釜夹套冷却水进水阀形成联锁控制,在氟化反应釜处设立紧急停车系统,当氟化反应釜内温度或压力超标或搅拌系统发生故障时自动停止加料并紧急停车。
(3)安全泄放系统。
(八)加氢工艺
1.反应类型:放热反应。
2.工艺危险特点:
(1)反应物料具有燃爆危险性,氢气的爆炸极限为4%~75%,具有高燃爆危险特性。
(2)加氢为强烈的放热反应,氢气在高温高压下与钢材接触,钢材内的碳分子易与氢气发生反应生成碳氢化合物,使钢制设备强度降低,发生氢脆。
(3)催化剂再生和活化过程中易引发爆炸。
(4)加氢反应尾气中有未完全反应的氢气和其他杂质在排放时易引发着火或爆炸。
3.重点监控单元:加氢反应釜、氢气压缩机。
4.宜采用的控制方式:
(1)将加氢反应釜内温度、压力与釜内搅拌电流、氢气流量、加氢反应釜夹套冷却水进水阀形成联锁关系,设立紧急停车系统。
(2)加入急冷氮气或氢气的系统。
(3)当加氢反应釜内温度或压力超标或搅拌系统发生故障时自动停止加氢,泄压,并进入紧急状态。
(4)安全泄放系统。
(九)重氮化工艺
1.反应类型:绝大多数是放热反应
2.工艺危险特点:
(1)重氮盐在温度稍高或光照的作用下,特别是含有硝基的重氮盐极易分解,有的甚至在室温时亦能分解。在干燥状态下,有些重氮盐不稳定,活性强,受热或摩擦、撞击等作用能发生分解甚至爆炸。
(2)重氮化生产过程所使用的亚硝酸钠是无机氧化剂,175℃时能发生分解、与有机物反应导致着火或爆炸。
(3)反应原料具有燃爆危险性。
3.重点监控单元:重氮化反应釜、后处理单元。
4.宜采用的控制方式:
(1)将重氮化反应釜内温度、压力与釜内搅拌、亚硝酸钠流量、重氮化反应釜夹套冷却水进水阀形成联锁关系,在重氮化反应釜处设立紧急停车系统,当重氮化反应釜内温度超标或搅拌系统发生故障时自动停止加料并紧急停车。安全泄放系统。
(2)重氮盐后处理设备应配置温度检测、搅拌、冷却联锁自动控制调节装置,干燥设备应配置温度测量、加热热源开关、惰性气体保护的联锁装置。
(3)安全设施,包括安全阀、爆破片、紧急放空阀等。
(十)氧化工艺
1.反应类型:放热反应。
2.工艺危险特点:
(1)反应原料及产品具有燃爆危险性。
(2)反应气相组成容易达到爆炸极限,具有闪爆危险。
(3)部分氧化剂具有燃爆危险性,如氯酸钾、高锰酸钾、铬酸酐等都属于氧化剂,如遇高温或受撞击、摩擦以及与有机物、酸类接触,皆能引起火灾爆炸。
(4)产物中易生成过氧化物,化学稳定性差,受高温、摩擦或撞击作用易分解、燃烧或爆炸。
3.重点监控单元:氧化反应釜。
4.宜采用的控制方式:
(1)将氧化反应釜内温度和压力与反应物的配比和流量、氧化反应釜夹套冷却水进水阀、紧急冷却系统形成联锁关系。
(2)在氧化反应釜处设立紧急停车系统,当氧化反应釜内温度超标或搅拌系统发生故障时自动停止加料并紧急停车。
(3)配备安全阀、爆破片等安全设施。
(十一)过氧化工艺
1.反应类型:吸热反应或放热反应。
2.工艺危险特点:
(1)过氧化物都含有过氧基(—O—O—),属含能物质,由于过氧键结合力弱,断裂时所需的能量不大,对热、振动、冲击或摩擦等都极为敏感,极易分解甚至爆炸。
(2)过氧化物与有机物、纤维接触时易发生氧化、产生火灾。
(3)反应气相组成容易达到爆炸极限,具有燃爆危险。
3.重点监控单元:过氧化反应釜。
4.宜采用的控制方式:
(1)将过氧化反应釜内温度与釜内搅拌电流、过氧化物流量、过氧化反应釜夹套冷却水进水阀形成联锁关系,设置紧急停车系统。
(2)过氧化反应系统应设置泄爆管和安全泄放系统。
(十二)胺基化工艺
1.反应类型:放热反应。
2.工艺危险特点:
(1)反应介质具有燃爆危险性。
(2)在常压下 20℃时,氨气的爆炸极限为 15%~27%,随着温度、压力的升高,爆炸极限的范围增大。因此,在一定的温度、压力和催化剂的作用下,氨的氧化反应放出大量热,一旦氨气与空气比失调,就可能发生爆炸事故。
(3)由于氨呈碱性,具有强腐蚀性,在混有少量水分或湿气的情况下无论是气态或液态氨都会与铜、银、锡、锌及其合金发生化学作用。
(4)氨易与氧化银或氧化汞反应生成爆炸性化合物(雷酸盐)。
3.重点监控单元:胺基化反应釜。
4.宜采用的控制方式:
(1)将胺基化反应釜内温度、压力与釜内搅拌、胺基化物料流量、胺基化反应釜夹套冷却水进水阀形成联锁关系,设置紧急停车系统。
(2)安全设施,包括安全阀、爆破片、单向阀及紧急切断装置等。
(十三)磺化工艺
1.反应类型:放热反应。
2.工艺危险特点:
(1)反应原料具有燃爆危险性;磺化剂具有氧化性、强腐蚀性;如果投料顺序颠倒、投料速度过快、搅拌不良、冷却效果不佳等,都有可能造成反应温度异常升高,使磺化反应变为燃烧反应,引起火灾或爆炸事故。
(2)氧化硫易冷凝堵管,泄漏后易形成酸雾,危害较大。
3.重点监控单元:磺化反应釜。
4.宜采用的控制方式:
(1)将磺化反应釜内温度与磺化剂流量、磺化反应釜夹套冷却水进水阀、釜内搅拌电流形成联锁关系,紧急断料系统,当磺化反应釜内各参数偏离工艺指标时,能自动报警、停止加料,甚至紧急停车。
(2)磺化反应系统应设有泄爆管和紧急排放系统。
(十四)聚合工艺
1.反应类型:放热反应。
2.工艺危险特点:
(1)聚合原料具有自聚和燃爆危险性。
(2)如果反应过程中热量不能及时移出,随物料温度上升,发生裂解和暴聚,所产生的热量使裂解和暴聚过程进一步加剧,进而引发反应器爆炸。
(3)部分聚合助剂危险性较大
3.重点监控单元:聚合反应釜、粉体聚合物料仓。
4.宜采用的控制方式:
(1)将聚合反应釜内温度、压力与釜内搅拌电流、聚合单体流量、引发剂加入量、聚合反应釜夹套冷却水进水阀形成联锁关系,在聚合反应釜处设立紧急停车系统。
(2)当反应超温、搅拌失效或冷却失效时,能及时加入聚合反应终止剂。
(3)安全泄放系统。
(十五)烷基化工艺
1.反应类型:放热反应。
2.工艺危险特点:
(1)反应介质具有燃爆危险性。
(2)烷基化催化剂具有自燃危险性,遇水剧烈反应,放出大量热量,容易引起火灾甚至爆炸。
(3)烷基化反应都是在加热条件下进行,原料、催化剂、烷基化剂等加料次序颠倒、加料速度过快或者搅拌中断停止等异常现象容易引起局部剧烈反应,造成跑料,引发火灾或爆炸事故。
3.重点监控单元:烷基化反应釜。
4.宜采用的控制方式:
(1)将烷基化反应釜内温度和压力与釜内搅拌、烷基化物料流量、烷基化反应釜夹套冷却水进水阀形成联锁关系,当烷基化反应釜内温度超标或搅拌系统发生故障时自动停止加料并紧急停车。
(2)安全设施包括安全阀、爆破片、紧急放空阀、单向阀及紧急切断装置等。
(十六)新型煤化工工艺
1.反应类型:放热反应。
2.工艺危险特点:
(1)反应介质涉及一氧化碳、氢气、甲烷、乙烯、丙烯等易燃气体,具有燃爆危险性
(2)反应过程多为高温、高压过程,易发生工艺介质泄漏,引发火灾、爆炸和一氧化碳中毒事故。
(3)反应过程可能形成爆炸性混合气体。
(4)多数煤化工新工艺反应速度快,放热量大,造成反应失控。
(5)反应中间产物不稳定,易造成分解爆炸。
3.重点监控单元:煤化气炉。
4.宜采用的控制方式:
(1)将进料流量、外取热蒸汽流量、外取热蒸汽包液位、H2/CO比例与反应器进料系统设立联锁关系,一旦发生异常工况启动联锁,紧急切断所有进料,开启事故蒸汽阀或氮气阀,迅速置换反应器内物料,并将反应器进行冷却、降温。
(2)安全设施,包括安全阀、防爆膜、紧急切断阀及紧急排放系统等。
(十七)电石生产工艺
1.反应类型:吸热反应。
2.工艺危险特点:
(1)电石炉工艺操作具有火灾、爆炸、烧伤、中毒、触电等危险性。
(2)电石遇水会发生激烈反应,生成乙炔气体,具有燃爆危险性。
(3)电石的冷却、破碎过程具有人身伤害、烫伤等危险性。
(4)反应产物一氧化碳有毒,与空气混合到12.5%~74%时会引起燃烧和爆炸。
(5)生产中漏糊造成电极软断时,会使炉气出口温度突然升高,炉内压力突然增大,造成严重的爆炸事故
3.重点监控单元:电石炉。
4.宜采用的控制方式:
(1)将炉气压力、净化总阀与放散阀形成联锁关系。
(2)将炉气组分氢、氧含量高与净化系统形成联锁关系。
(3)将料仓超料位、氢含量与停炉形成联锁关系。
(4)安全设施,包括安全阀、重力泄压阀、紧急放空阀、防爆膜等。
(十八)偶氮化工艺
1.反应类型:放热反应。
2.工艺危险特点:
(1)部分偶氮化合物极不稳定,活性强,受热或摩擦、撞击等作用能发生分解甚至爆炸。
(2)偶氮化生产过程所使用的肼类化合物,高毒,具有腐蚀性,易发生分解爆炸,遇氧化剂能自燃。
(3)反应原料具有燃爆危险性。
3.重点监控单元:偶氮化反应釜、后处理单元。
4.宜采用的控制方式:
(1)将偶氮化反应釜内温度、压力与釜内搅拌、肼流量、偶氮化反应釜夹套冷却水进水阀形成联锁关系。在偶氮化反应釜处设立紧急停车系统,当偶氮化反应釜内温度超标或搅拌系统发生故障时,自动停止加料,并紧急停车。
(2)后处理设备应配置温度检测、搅拌、冷却联锁自动控制调节装置,干燥设备应配置温度测量、加热热源开关、惰性气体保护的联锁装置。
(3)安全设施,包括安全阀、爆破片、紧急放空阀等
- 扫码加建筑类考试老师微信
- 进行“一对一”考试资讯
-
注意:
-
.在添加客服时,备注自己要咨询的【考试种类+地区】
-
.先添加客服,再由客服按实际情况推荐给考试老师
-
.添加老师可咨询:考试信息+考试资料+交流群推荐


-
2019安全工程师《化工安全》第一章要点:化学品的标志、标签 2021/12/24
-
2019注册安全工程师《化工安全》第二章考点:重点监管的化工工艺及主要安全技术措施 2021/12/24
-
2019注册安全工程师《化工安全》第二章考点:精细化工工艺危险性及安全技术措施 2021/12/24
-
2020年中级安全工程师考试《化工安全》考点讲义:化学品安全标签 2021/12/24
-
2020年中级安全工程师考试《化工安全》考点讲义:光气及光气化工艺 2021/12/24
-
2020年中级安全工程师考试《化工安全》考点讲义:电解工艺 2021/12/24
-
2021年中级安全工程师《化工安全》章节知识点:化工安全生产概述 2021/12/24
-
2021年中级安全工程师《化工安全》章节知识点:化工运行安全技术 2021/12/01
-
2021年中级安全工程师《化工安全》章节知识点:化工防火防爆安全技术 2021/12/01
-
2021年中级安全工程师《化工安全》章节知识点:化学品储运安全技术 2021/12/01

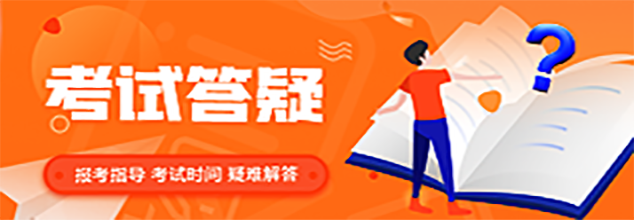
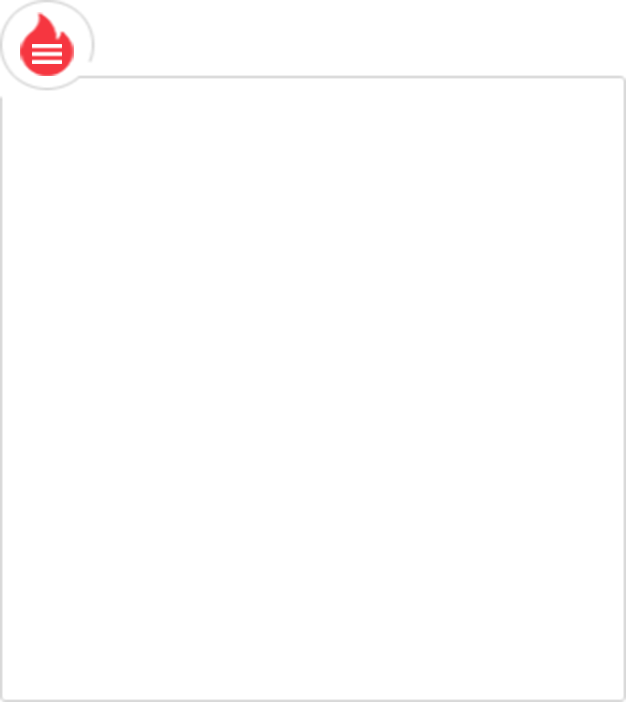